Le béton est composé à partir d’un mélange de ciment, de granulat et d’eau. D’autres éléments peuvent être intégrés: adjuvant, ajout, additif. Info composition. Dosage pour 1m3 de béton.
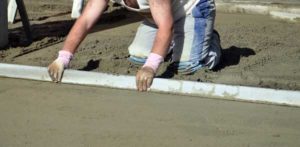
La formulation du béton
Le béton est fabriqué avec trois composants basiques: l’eau, le granulat (sable, gravier) et le ciment.
Bétonnière en action !
Ce mélange est alors coulé, puis il durcit; avant de se transformer dans le matériau que nous connaissons tous.
En plus des constituants de base, d’autres éléments peuvent entrer dans la composition du béton : adjuvant, ajout et addition.
Ces éléments permettent d’atteindre des propriétés supplémentaires: résistance, coloration, perméabilité, ou encore, fluidité.
Nous détaillerons chacun des constituants qui peuvent entrer dans la composition d’un béton, tout en prenant soin de bien préciser leur utilité.
Le ciment pour béton
Beaucoup de gens confondent le ciment et le béton. Pourtant ces matériaux ne sont pas pareils.
Le ciment est une poudre fine de couleur grise ou blanche qui durcit en présence d’eau.
C’est l’un des éléments de composition du béton.
Il assure un rôle primordial, puisqu’il constitue le liant principal du béton i.e. il assure la cohésion des composants.
Il existe beaucoup de variétés de ciment. Le plus commun est le ciment de portland. Celui-ci est obtenu à partir d’un mélange de calcaire (80%) et d’argile (20%).
Le dosage du ciment dans le béton
Le dosage d’un ciment est exprimé en kg/m3.
Pour une application courante, le dosage en ciment évolue entre ~250 kg/m3 à 400 kg/m3.
- Dosage ciment à 250 kg/m3: béton de propreté
- Dosage ciment à 300 kg/m3 : dalle piétonne, terrasse, cour, fondation superficielle
- Dosage ciment à 350 kg/m3: fondation, dalle carrossable, poteau
- Dosage ciment à 400 kg/m3: poteau, poutre, ouvrage en béton armé
L’eau
L’eau est indispensable à la fabrication du béton. Son rôle est double, puisqu’elle permet à la fois d’hydrater le ciment (25%), et d’apporter la fluidité désirée (75%).
- L’hydratation du ciment : l’eau entraine la prise du ciment et le durcissement du béton.
- La fluidité : l’eau permet d’obtenir un matériau malléable, qui peut être coulé dans un coffrage. En revanche, elle doit être dosée avec précaution, sans quoi elle peut entrainer une perte de résistance.
Dosage de l’eau dans le béton
L’eau entre dans la composition du béton à hauteur de ~120 à 200 litres par mètre cube de béton.
Le dosage doit être précis, puisque tout excédent occasionne une perte de résistance du béton (l’ajout de ~10 litres/m3 à un béton de chantier =~ -4 MPa)
Outre la perte de résistance, d’autres effets secondaires peuvent être occasionnés par un excès d’eau.
- Etat de surface dégradé : fissures et « bullage »
- Augmentation de la porosité du béton (évaporation de l’excédent)
- Retrait augmenté du béton (nécessité de mettre des joints)
Pour obtenir un béton très malléable, sans perte mécanique, on peut utiliser un produit plastifiant en lieu et place de l’eau.
Le granulat
Le granulat est composé de grains minéraux de tailles variables, dont les plus communs portent les noms de “sable” et de “gravier”. Ils entrent dans la composition du béton et le mortier.
Le sable et le gravier pour béton
Le sable et le gravier constituent le « squelette » du béton. Ils contribuent pleinement à la résistance du matériau.
La taille des sables et des graviers est déterminée par utilisation d’un tamis.
Une fois tamisé, le granulat est défini par un rapport « d/D », dont « d » représente la taille des plus petits grains et « D », celle des plus gros grains.
Ainsi, suivant la taille des grains, le granulat porte différentes appellations : filler, sable, grave, gravillon et ballast.
- Le filler : 0 à 0.063 mm
- Le sablon : 0 à 1 mm
- Le sable : 0/D et D ≤ 4 mm
- Le gravillon : d /D d ≥ 2mm et 4 ≤ D ≤ 63 mm
- La grave : mélange de sable et de gravillon
L’origine des « cailloux »
Les « cailloux » présents dans le béton sont issus de carrières de roches alluvionnaires ou massives.
- La roche alluvionnaire : il s’agit de granulats « roulés », qui sont issus des cours d’eau. Ils présentent ainsi un aspect « poli » à l’état naturel.
- La roche massive : elle est issue de carrières et extraite par des techniques telles que le dynamitage. La roche est ensuite « fragmentée » en vue d’obtenir des grains de tailles maitrisées (concassage).
A noter qu’il existe également de granulats spéciaux, d’origine naturelle ou artificielle, qui peuvent être employés pour réaliser des bétons. C’est notamment le cas du schiste expansé, ou des billes de polystyrène.
La masse volumique du granulat
Sans « surprise », le granulat est un matériau « pondéral ». En effet, la masse volumique du produit « en vrac » est de l’ordre de 1400 à 1600 kg/m3 (suivant qu’il s’agit d’un sable ou d’un caillou).
En excluant les vides, elle se situe entre ~2500 et ~2700 kg/m3.
Bétons spéciaux et granulats
Le granulat est l’un des « leviers » sur lesquels les professionnels du béton travaillent pour réaliser des « produits spéciaux ».
Voici quelques exemples de bétons qui nécessitent un choix judicieux de sable et de gravier.
- Le béton décoratif : il utilise des minéraux colorés, pour offrir un bel aspect visuel;
- Le béton drainant: il est réalisé à partir de classes granulaires fortement discontinues;
- Le béton léger : il incorpore des granulats légers (billes d’argile, polystyrène);
- Le béton à forte densité: il inclut des petites particules pour combler les vides;
L’adjuvant pour béton
L’adjuvant est un produit qui est incorporé au moment du mélange du béton. Il en améliore les caractéristiques à l’état frais ou durci.
Son dosage est inférieur à ~5% de la masse du poids de ciment.
Il intervient sur plusieurs paramètres : la résistance, la fluidité, le temps de prise, la perméabilité.
- La fluidité : elle est apportée par les plastifiants et les super-plastifiants. Ces produits accroissent également la résistance du béton à l’état durci.
- Le temps de prise: il peut être régulé par intégration d’un accélérateur ou d’un retardateur de prise.
- La perméabilité : elle peut être augmentée par l’incorporation d’un entraineur d’air, qui créée des microbulles dans le béton. A l’inverse, l’hydrofuge de masse limite la pénétration de l’eau dans les pores et les capillaires du béton.
Les ajouts
Le béton fibré est réalisé grâce à un ajout de fibres lors du mélange du béton
Les ajouts désignent tous les éléments supplémentaires qui entrent dans la composition d’un béton, en vue d’en améliorer les propriétés.
Parmi-eux, il est possible de citer les éléments ci-dessous.
- La fibre: elle peut être synthétique ou métallique. La fibre accroit la résistance du béton, et elle évite la diffusion des fissures. Pour certaines applications, les fibres remplacent les armatures.
- Le colorant : il embellit le béton; dans la masse ou en surface !
Les additions
Les additions sont des très petites particules, qui sont intégrées dans le béton pour augmenter le volume de pâte, et combler les vides.
Ils aboutissent à un béton plus compact et plus résistant.
L’addition se répartit en plusieurs catégories: le filler, la cendre, le laitier et la fumée.
- Le filler : il s’agit d’un très petit granulat. Le mot « filler » vient de l’anglais « to fill », qui signifie remplir. Le filler comble les petits trous/capillaires présents dans le béton; pour en améliorer les propriétés.
- Les cendre, laitiers et fumées: il s’agit de coproduits issus de l’industrie (laitier de haut fourneau, fumée de silice, cendre volante).
Le dosage du béton
Pour un béton « courant », on utilise les dosages ci-dessous (tableau indicatif pour 1m3 de béton – donné à titre indicatif).
Application | Dosage en ciment (kg) | Sable 0/5 (L) | Gravier 5/20 (L) | Dosage en eau (L) |
Dalle piétonne, fondation superficielle | 300 | 520 | 730 | 155 |
Dalle carrossable, sol garage, plancher, poutre, poteau, fondation | 350 | 500 | 700 | 175 |
Béton armé | 400 | 450 | 650 | 195 |
Pour les bétons spéciaux, le dosage en compléments (adjuvant, ajout, addition) se fait au cas par cas. Les dosages sont souvent donnés par les fabricants des produits.
Cela étant dit, la préparation d’un béton à valeur ajoutée est bien souvent du ressort d’une centrale à béton, qui en maîtrise toutes les subtilités.
Un tel béton est commandé en centrale, puis livré par camion toupie. A la sortie du camion, le béton est « tout prêt » : il ne nécessite pas de traitement ultérieur.
Besoin de sable ou gravier ?